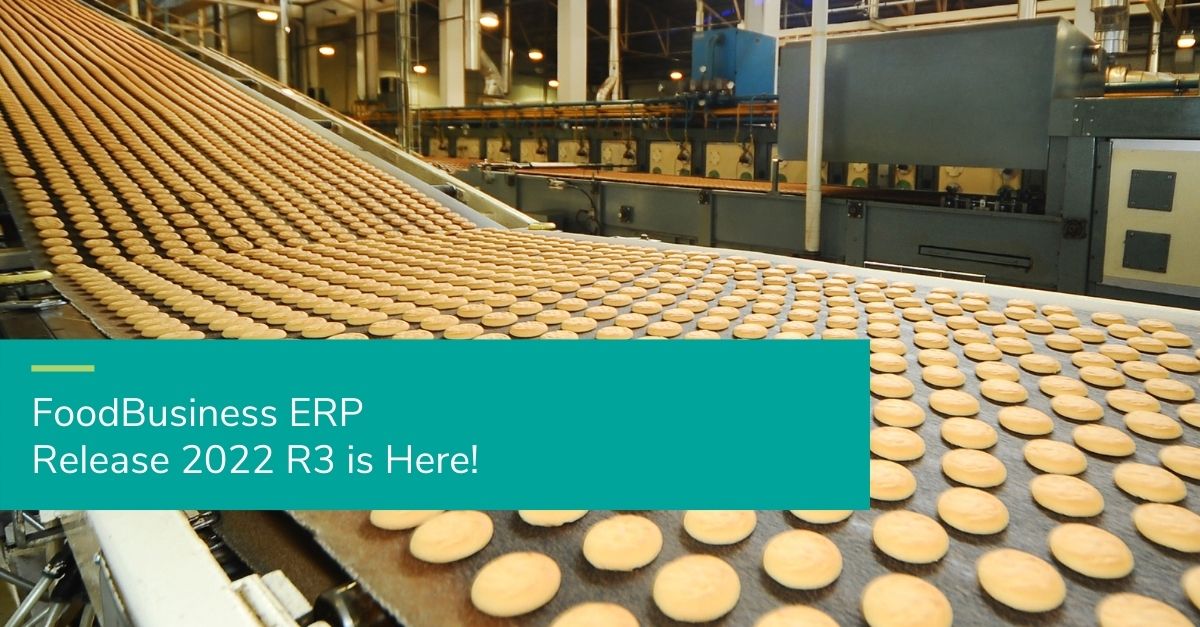
Quality from the Start
Companies have invested significantly in building their company, brand, and products. An effective quality program is an essential component of protecting these valuable assets. Mistakes can be costly to both your bottom line and reputation. FoodBusiness ERP supports our customers by providing quality-focused features that go beyond normal ERP transactions. We started this journey by introducing quality audits to provide robust functionality, which supports the quality team and its programs. The audit functionality, combined with sound business processes, can be used to meet industry standards and certifications such as GMP, HAACP, SFCR, GFSI, etc. To support those programs and facilitate the management of supplier documents, we added the ability to proactively manage required supplier documentation and expiration. The theme continued with the introduction of stock quality audits. This homogenized the setup and management of the audits with inventory control (stock audits) and holds. FoodBusiness ERP 2022 R3 continues this theme by introducing advanced Certificate of Analysis (COA) features to support deliveries and receipts.
Customer Support and Deliveries
It is not unusual to have quality requirements, terminology and acceptance standards that differ from your customer’s. FoodBusiness ERP recognizes this complexity and helps you manage these requirements. The outbound COA publication process allows you to define a COA that matches your company standards. This document may contain all or a subset of the test group. While this is a good start, we took it a step further and provided the ability to define customer-specific COA documents.
When test results are captured in a stock quality audit (test group), they may contain tests or test results that are not intended for or required by external audiences. The new COA functionality provides multiple controls for managing and controlling the COA content.
- Document specific test descriptions
- Group similar tests
- Omit a test or result
- Include the test method
- Display results based on a numeric test result
Customers often have specific requirements for the COA, and how they want to see the results presented. FoodBusiness ERP supports this by providing configuration tools that allow your customers to “have it their way.” This is not limited to the tests that appear on the document but also the verbiage used. This provides essential quality data in a format that is easily digested and understood by the recipient. The only requirement is that the individual tests must be included in the stock audit/test group.
Companies often have many finished or semi-finished products that are produced from a batch or intermediate formulation. When that is the case, the quality testing is typically done at the batch level, and not on the finished item. There are many production scenarios where this occurs such as differences in package size, branded product vs. private label, etc. Those use cases often present challenges for generating the COA. That is not the case for FoodBusiness ERP because it contains lot inheritance logic that will trace the finished product back to the source batch that was tested. The inheritance logic allows you to structure your formulas or BOMs in the manner that is best for your organization with no negative impacts on your COA processing.
Many different options have been mentioned when discussing the COA document (custom text, omission of certain tests, value or summarized results, grouping, company standard, customer-specific, etc.). Choices and options can sometimes be overwhelming and make the setup appear to be a difficult and tedious process. To simplify the setup, FoodBusiness ERP provides a simulated option, which provides real-time feedback and setup validation with the click of a button.
FoodBusiness ERP provides multiple options for printing a COA document. The most common case would be based on a delivery. A delivery can be comprised of a mixture of products and lots – some of which may require a COA, others may not. The COA produced will use the setup and create a document for each lot being delivered that requires a COA. The documents can be printed and sent with the carrier or captured in an electronic friendly format (PDF) for distribution via other means such as email.
COA printing is not limited to deliveries. A COA can be printed for any stock belonging to a product that has been tested, and that is set up for COA processing. This provides support for scenarios such as creating a pre-order sample for a prospect or customer, or selecting stock to use for special projects like validating alternate formulations or performing production trials.
Pre-Receipt COA
Companies often purchase products for resale or for use in their own production process. Your purchase agreements may require your supplier to provide test results (COA), or a pre-shipment sample for approval. This data is often available prior to the delivery. When that is the case, the Pre-Receipt COA feature allows you to record the quality data in advance, and streamline the receipt activity. Typical processing places a quality hold on the inventory received until the quality data is recorded, which can cause delays in production or fulfillment activities. If COA results are present, the Pre-Receipt COA feature enables the receipt process to be as simple as an inspection allowing the hold process to be bypassed.
If you are interested in learning more about FoodBusiness ERP and how it can help your organization, contact our experts today. We’d love to chat.