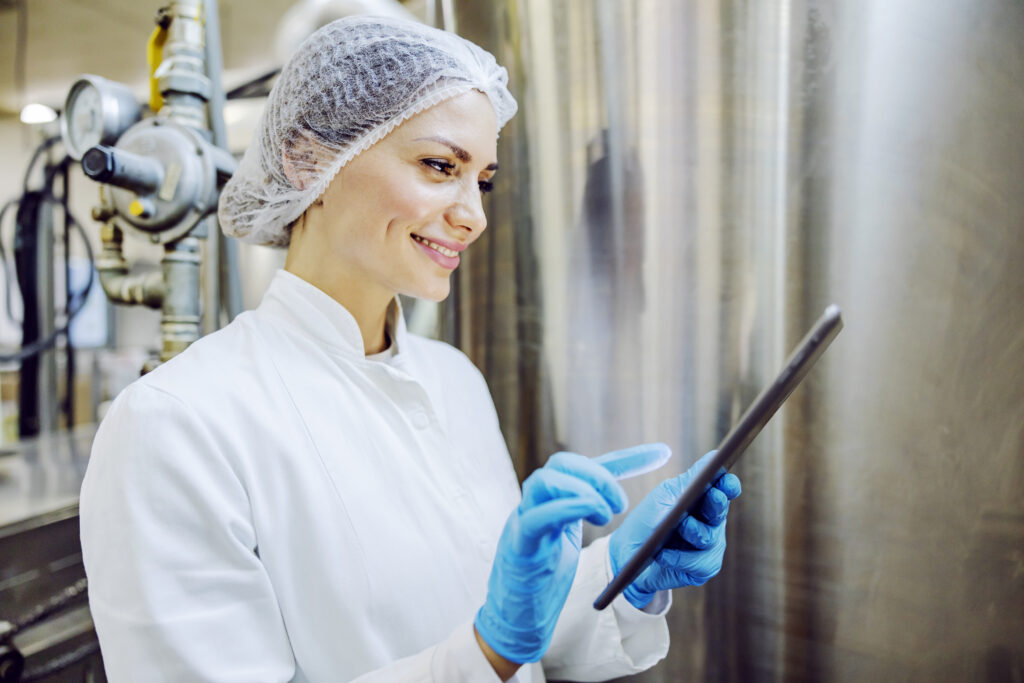
The food and beverage industry hasn’t been immune to the volatility of the past couple years. As the world continues to grapple with the aftermath of the COVID-19 pandemic, issues including inflation, supply chain problems and the war in Eastern Europe have created new struggles for food and beverage manufacturers.
Since last year, grocery prices have jumped 12% as food companies have been forced to raise prices to account for the cost of ingredients, packaging and other expenses. The big question for 2023, according to Food Processing, is how much can food and beverage companies continue these price hikes before consumers begin to resist?
Fortunately, food manufacturers may have other options when it comes to reducing their operating costs and achieving a lean approach to operations. A software solution purpose-built for the food industry provides manufacturers with the functionality and features they need to streamline processes, reduce waste, capitalize on sales opportunities and ensure quality.
FoodBusiness ERP is software designed for food and beverage manufacturers. It is a single system designed to manage every aspect of a business, including production and operations, finance, food safety, compliance, quality, traceability and more. FoodBusiness ERP 2023 R1 is the latest version and includes even more of the functionality food manufacturers need to navigate economic volatility and come out ahead.
Keep reading to learn about some of the new features included in this latest release.
Built to Make Food Even Better
FoodBusiness ERP is built in Sage X3 and developed from years of industry experience incorporating best practices from food and beverage leaders across North America. To make food better, FoodBusiness ERP technology experts have created even more features to help customers adapt to changing industry trends and stay competitive.
Here’s a look at some of the new features included in FoodBusiness ERP 2023 R1:
1. Customer-Specific Allocation
In our FoodBusiness ERP 2022 R3 release, we focused on advanced Certificate of Analysis (COA) features to support deliveries and receipts and take the complexity out of managing these requirements. In this latest version of FoodBusiness ERP, our development team took this functionality a step further.
Unlike other generic ERP solutions, FoodBusiness ERP works to simplify customer-specific requirements in the allocation process. For example, if a customer has test result requirements that exceed a company’s standard for acceptance, instead of having to perform additional steps or manual processes to ensure that the stock or lots delivered are acceptable, FoodBusiness ERP has an option to manage this customer specific allocation automatically.
The solution does this by first checking to see if a customer has specific COA requirements for a product. If those requirements are present, they are applied to the allocated stock to ensure that it meets this customer’s criteria. On top of this, FoodBusiness ERP also allows an authorized user to manually override the customer-specific allocation to handle an exception with customer acceptance.
2. Rebates and Royalties
To ensure success in a volatile market, food manufacturers must have a sales program in place that boosts customer satisfaction and overall company profits. Even the best manufacturing companies with world-class production, distribution and supply chain operations will suffer without the ability to successfully launch and manage a sales program.
With FoodBusiness ERP, customers have the tools needed to set up, calculate and pay rebates and royalties with ease. Instead of relying on time-consuming and error-prone manual tasks to run a successful rebate and royalty program, FoodBusiness ERP customers can streamline the process, which allows staff to focus on strategic initiatives and value-added activities.
i) Rebates
FoodBusiness ERP’s rebate solution supports rebate processing by providing users with a flexible framework for defining and managing sales programs. It is fully integrated with FoodBusiness ERP’s fulfillment and accounting modules, giving the accounting department flexibility and control over GL account and dimensions used to track a sales program. FoodBusiness ERP users get access to real-time information about their rebate programs, including the rebates that apply to sales lines, program status and calculated benefits, and the program results, which can be viewed graphically or numerically.
ii) Royalties
Royalties are typically paid due to trademarks, ownership, branding (and more) for certain products a business sells. FoodBusiness ERP 2023 R1 supports royalty processing by providing a flexible framework that is integrated with the fulfillment process for real-time tracking. It provides options for how users manage the benefit from an accounting perspective, as well as how to reimburse a supplier or licensor.
In FoodBusiness ERP 2023 R1, users address paying a royalty to an external party based on sales. Depending on how the business sets up the royalty program, royalties can be paid by:
- A fixed price per unit
- A percent based on gross or net price
The royalty program lets users track royalties through the sales, delivery and invoice process while also allowing them to define the payments periods (e.g., monthly, quarterly, etc.).
iii) Benefit Management
FoodBusiness ERP’s Program Payment Workbench is designed to simplify the management of rebate and royalty benefits. The workbench uses program data to present benefits that need to be processed, which will result in either a customer credit invoice or a supplier invoice for payment. Managing the benefit at the invoice level allows benefits to be processed as part of the normal accounting operations for accounts receivable and accounts payable.
3. Work in Progress Audits/Groups
Quality management is always critically important to food and beverage manufacturers, which is why we continue to build functionality addressing quality audits in our new releases. In the past, we developed manual, event-based and frequency audits to support quality management throughout the production process. Now, we’re excited to introduce Work in Progress (WIP) audits. These audits are designed to automate and collate WIP production testing done by different departments, with varying objectives – including equipment monitoring, environmental control or product characteristics – and at various frequencies. With this functionality, users get the insight, visibility and control they need to monitor WIP proactively before a batch is finished and may be unusable.
On top of this, FoodBusiness ERP 2023 R1 introduces a new feature called Audit Groups, which are designed to provide quality teams with the flexibility they require during production. Audit Groups are a collection of checklists or parameters that allow for multiple audits or even multiple occurrences of a single audit within that specific audit group. These Audit Groups can be created for individual work orders or jobs and help streamline quality data collection and overall quality visibility.
To learn how your food and beverage company can reduce operating costs, streamline operations and manage business growth reach out to us. We’d love to show you what FoodBusiness ERP can do for your business.