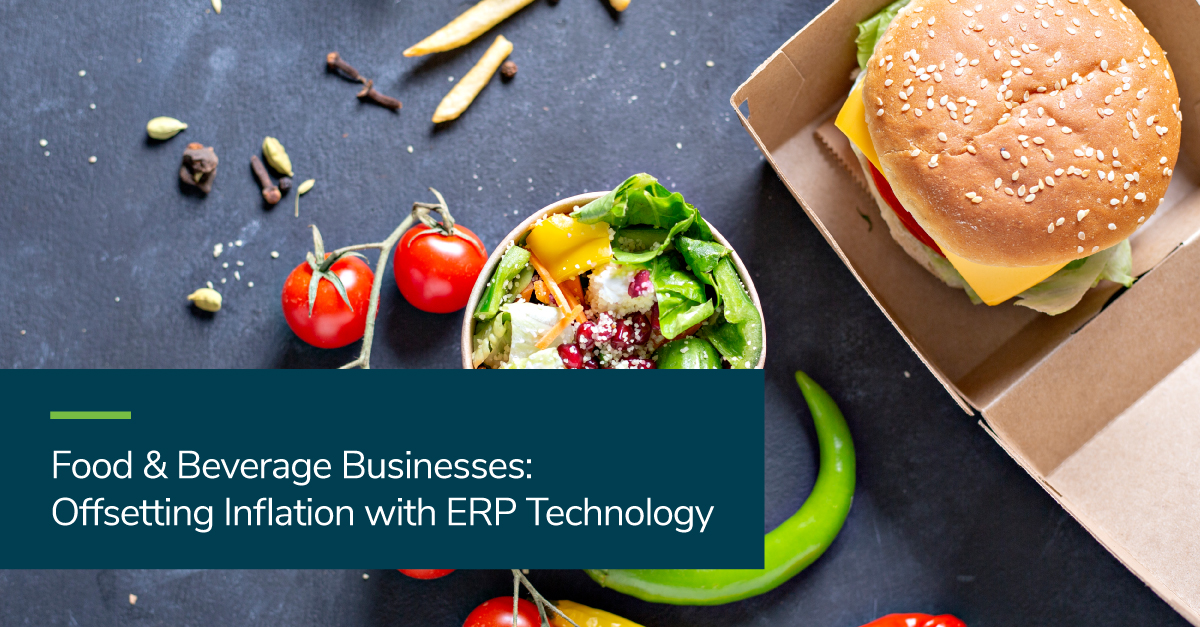
Seven out of 10 people consider inflation the top concern facing the US today. With an overall inflation rate of 9.1%, there’s reason to be concerned—especially within the food and beverage industry. Food and beverage manufacturers are feeling the pressure as their costs continue to swell in response to inflation, as well as to ongoing labor shortages and supply chain disruptions. In response, savvy industry professionals must save money.
Saving money sounds great! But how?
Inflation Woes Eased With Food Manufacturing Software
The first step is to look at your food production and distribution processes to find where you can streamline and find efficiencies. This is where food manufacturing software, like FoodBusiness ERP, will really come in handy. FoodBusiness ERP is built to help food manufacturers, processors and distributors streamline manufacturing, inventory, production and operational costs – all welcome benefits in the tide of rising inflation
Let’s look at this immediate and value-filled functionality through the eyes of real FoodBusiness ERP customers who are already experiencing the solution’s cost-saving benefits—and easing their inflation woes in the process.
Elmer Candy Corporation
Since 1855, Elmer Candy Corporation has been providing seasonal boxed chocolate to customers across the nation. Its assorted chocolates are made in the U.S. and can be found in major retail stores, such as Walmart, Costco, Kroger and Target.
The thriving company decided it needed modern technology to help them efficiently meet growing demand. With the help of NexTec experts, Elmer Candy implemented its end-to-end solution that resulted in a number of benefits. The team now receives real-time data, which helps them make rapid decisions. And the team knows exactly which products are in stock through integrated and detailed inventory tracking, leading to accurate ordering information and to the reduction of overstocking and waste.
Says Joseph Wiley, MIS Director, “We can quickly and easily trace raw ingredients from initial receipt through final sale.”
As a food manufacturer, lot traceability is essential. So are the “visible and measurable” cost savings that have occurred since the company implemented its modern ERP solution.
“Through labor savings, quicker turnaround, improved accuracy, strategic purchasing, and streamlined processes, we are in a position to grow the business 10 to 15 percent without adding additional resources,” Wiley says.
Ara Food Corp
Ara Food Corp has been manufacturing plantain and cassava chips for over 40 years. According to its website, the company is the largest manufacturer of this “alternative snack” (which is Kosher friendly, SQF Certified, and recognized by the Global Food Safety Initiative) in the U.S.
After Ara Food Corp implemented FoodBusiness ERP, the company was able to access real-time data, transforming its accounting procedures. “Previously, we spent the next day keying all the production data into our software. Now, we have laptops on the shop floor and are capturing manufacturing data in real time—when and where it’s happening,” says Marta De Varona, VP Finance and Administration.
Ara Food Corp, as a make-to-order enterprise, uses FoodBusiness ERP’s food business software to manage its food manufacturing production requirements, including reducing the number of days it takes to get its product from production to delivery and using its intelligence capabilities to optimize their inventory and resource management. Complying with quality and food safety requirements is also simplified with bidirectional ingredient and product traceability, quality checks, allergen management and expiration date tracking.
Because of these increased efficiencies, Ara Food Corp is saving time and money. And it’s saving even more money through the cost tracking capabilities.
“We’re now able to track scrap and waste in ways that weren’t feasible before. It’s been very helpful both in honing our own practices, and also to match scrap and waste back to the source of the plantains,” De Varona says. “We’ve identified suppliers from which we receive a higher amount of scrap and waste and work with them to help them improve their handling procedures.”
Milo’s Tea Company
Milo’s Tea Company is a family-owned, zero-waste manufacturing business that is also a Certified Women Owned Business located in Bessemer, Alabama. Its teas and lemonade beverages, which are made from natural ingredients, are the “heart and soul” of Milo’s.
The company’s decision to implement food manufacturing software was predicated on the need to improve efficiency with automation. Darlyne Hagood, Director of Administration, says they had to manage time zone conversions manually, which, when producing a perishable product, was a concern. With the food manufacturing software, they were able to automate the conversion process as well as enjoy multi-currency support.
The improved efficiency ensured that Milo’s was able to track its ingredients, including expiration dates, easily and accurately. And this easy, accurate tracking reduced the incidence of lost inventory—saving them money in the process.
About FoodBusiness ERP
Though the ongoing challenges brought on by inflation and supply chain disruptions were not the reasons these three businesses chose FoodBusiness ERP, their decision has equipped them to handle these challenges—and any other challenges—with ease.
Some benefits of FoodBusiness ERP are:
- Quicker turnarounds
- Improved accuracy
- Strategic purchasing
- Automated processes
- Accurate demand forecasting
- Detailed cost tracking
- Real-time food manufacturing inventory management
- And more
Built in Sage X3 and configured by NexTec experts, FoodBusiness ERP delivers a complete food and beverage manufacturing business solution. To learn more, contact our experts today. We’d love to chat.