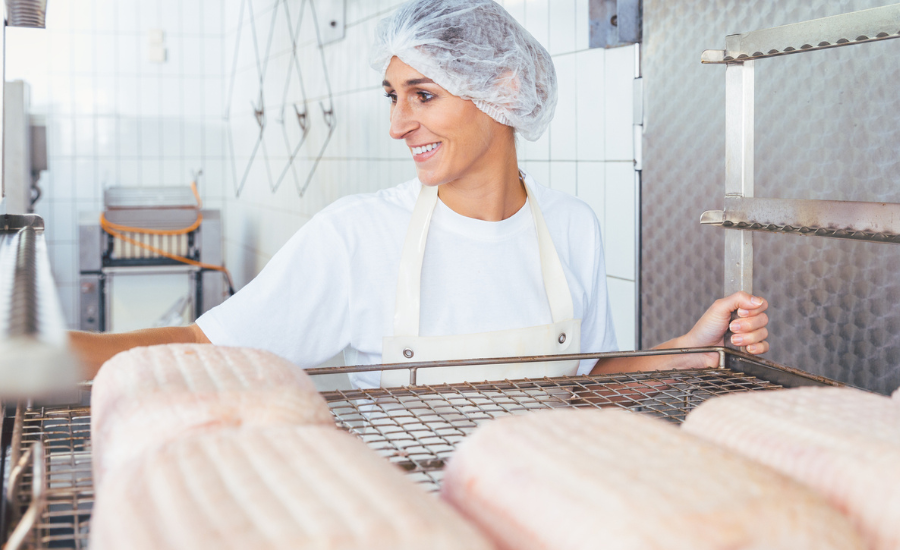
We hear it from our food and beverage customers all the time: “We need help managing our catch weights” and we get it! Catch weight management is difficult and can have a direct impact on both your bottom line and customer satisfaction if not managed correctly.
So how do food manufacturers – specifically meat, seafood, produce and cheese processors – accurately account for catch weight? The key is to have the tools in place to weigh, price and track a product throughout its supply chain lifecycle. From there, you can ensure that you’re recording the weight of individual items accurately and then pricing them accordingly.
In this blog, we answer the following questions:
- What is catch weight?
- Why is catch weight so important in food manufacturing?
- How do I effectively manage catch weight?
- How does ERP software accurately manage catch weight?
- Why is flexibility important to efficient catch weight management?
Ready to talk to one of our experts about our catch weight solution? Reach out for a quick and free demo.
First Things First: What is Catch Weight?
Simply put, catch weight is a food industry term that refers to the actual weight of an individual product. In meat, seafood, produce and cheese processing, the weight of each individual product will naturally vary in weight and size, and thus will need to be priced according to this variable weight. A good example is a porkchop, which is priced based on the weight of the actual piece of meat, not as a single porkchop with a fixed unit price.
These food items are typically sold by the case and by their catch weights. The actual weight inside the case may be slightly more or slightly less than the item’s average weight, and food manufacturers must have the tools to account for these variations in weight.
Another example is two packages of chicken breasts. Each package will inevitably vary in weight and size depending on how the chicken was broken down during processing. Although both packages may contain 6 chicken breasts, the unit price of the package must reflect the actual weight of the product inside the package and not the number of pieces. If a discrepancy between the unit price and the catch weight price occurs, the processor risks losing money or charging customers too much.
Let’s take a closer look at why accounting for catch weight is critical.
Why is Catch Weight So Important in Food Manufacturing?
Accurately measuring catch weight is not easy. But the importance of it is critical. Here’s why:
1. Accurate Pricing
For many food manufacturers, margins are tight. That means that without the ability to recoup the actual value of your items, you could be missing out on big profits. To price variable weight items fairly, you need to know the weight of individual pieces of product.
Relying on average weights and corresponding prices is likely to shortchange either you or your customer. That’s because if you sold your salmon steaks as though they all weigh the same, you would lose out on the value of the pieces that weigh more than the average price. On the flip side, charging customers too much for pieces that weigh less than the average price could hurt your brand.
2. Improved Production
Food manufacturers need complete visibility into inventory and production to operate at maximum efficiency. That’s why it’s important to have the tools to track exactly how much product is going in and out of your facilities.
Accurately accounting for catch weights helps manufacturers better measure the amount of product being sold, and then correlate that figure with data from other departments, such as production or finance. From there, business leaders can uncover strategies for fine-tuning the manufacturing process to save time, resources and money.
3. Buyer Satisfaction
So much of being a successful food manufacturer is ensuring customer satisfaction. To do this, producers of variable weight items need to be fair in their pricing. That means charging customers accurately for what they purchase.
Transparency is always key in food manufacturing, which is why it’s important for consumers to have no doubt that they are getting exactly what they are paying for. Catch weight functionality allows companies to account for differences in pricing in a clear and concise way, which helps ensure the integrity of your products.
In many cases, producers will include the actual weight of a product on the package label to be as transparent about pricing as possible.

How to Manage Catch Weight
If you’re currently managing catch weight using manual processes, you’re not alone. We often work with companies that stop production lines to manually record the weights of every package that comes through. These manual processes are prone to human error and can be incredibly costly in time and resources.
While this may work for growing businesses with fewer transactions and a smaller customer base, as a company grows so too does its need for a solution that automates the capturing, weighing and labeling processes that are integral to effectively managing catch weights.
Utilizing a software solution for catch weight management will help ensure pricing accuracy and production efficiency, in turn leading to more satisfied customers and increased sales.
Here’s more about how an automated solution for managing catch weights – or an Enterprise Resource Planning (ERP) solution with built-in catch weight functionality – works.
Catch Weight Automation and ERP Software
ERP software combines a company’s data, departments and processes into a single system. The result is streamlined operations and real-time visibility into company-wide data.
For managing catch weights, ERP software integrates every step of the catch weight management process into core modules of the software. That means that catch weights are measured and managed from the time a product is purchased, to when it is fulfilled, produced and then delivered. The result is full transparency and ultimate catch weight control.
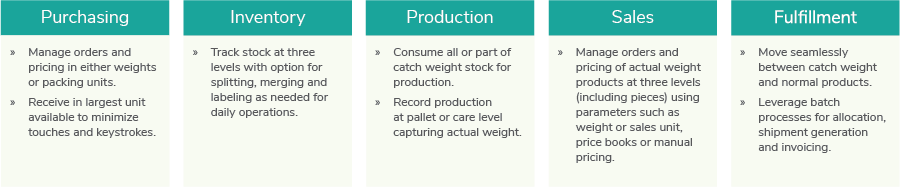
Because ERP software utilizes a single, unified database to manage a company’s operations, users can easily log the weight of goods when they are initially purchased and ensure that weight remains tied to the product throughout its lifecycle.
On top of this, an ERP solution that enables Automated Data Collection (ADC) functionality takes catch weight management a step further by allowing users to scan barcodes, perform transactions and manage products at the pallet or case level using a mobile device. With this, users can guarantee greater efficiency and next-level data accuracy since shop-floor data is being relayed directly to the ERP system.
Why Flexibility is Key to Efficient Catch Weight Management
It’s important to understand that not all catch weight management solutions are built the same. For our larger customers who come to us with legacy systems or proprietary software in place, we work closely with them to implement best practices and provide an additional level of production efficiency using ERP software built specifically for food manufacturing.
Only software built with the needs of food and beverage businesses in mind will come equipped with the functionality you need to address all your catch weight challenges.
Here’s why:
By implementing a system that is flexible in the way it measures product coming into your facility – for example, a solution like Sage X3 that can inherently manage multiple units of measure – users can minimize the overhead and resources it takes to track each case and its actual weight throughout production.
How Industry-Specific Software Streamlines Catch Weight Management
A system built for food and beverage manufacturing provides flexibility by allowing multiple levels of weight tracking when possible, including by pallet, case and piece. At purchasing, for example, users can enter product into their solution using the actual weight of the largest unit of measure, such as pallet or case. This flexibility simplifies the receiving process and increases efficiency, since the software doesn’t require you to track actual weights in smaller units until a breakdown is required to meet customer demand or when your processes require smaller units.
Then, when required, users have the tools to record the actual product weight at lower unit of measure and the system will adjust the original weight and new unit field accordingly. New labels will subsequently be produced reflecting the adjustment.
Let’s look at an example. Your company purchases a pallet of 50 cases of 6oz. ribeye steaks. Each case comes with a label that includes the weight of the case. While some businesses may choose to enter the weight of each individual case into its operating system, the process can be extremely cumbersome and time-consuming. Instead, a solution like FoodBusiness ERP allows users to log the average weight of the pallet when it is received, then break it down by its actual weights later in production when necessary.
The result is a more streamlined and efficient approach to managing catch weights.
Conclusion
Managing catch weights is a complex but essential part of your food processing business. If you’re not properly accounting for catch weights throughout a product’s lifecycle, you could be losing money and threatening customer satisfaction.
On the flip side, if you’re spending too much time unnecessarily tracking actual product weights in smaller units of measure, your business is likely not running as efficiently as possible.
To streamline your catch weight processes, lean on industry tools – like ERP software created for the food and beverage business – for your catch weight management needs.